Sauber Motorsport AG – Fresh air for C42
Aerodynamics in Formula 1 are decisive factors that determine vital hundredths of a second and also largely determine the car's design. Interesting new regulations have been the driving factor behind new airflows this season.
When you see what kind of air masses a Formula 1 car displaces during a race, you realise that every single detail in the aerodynamics is crucial. Minor modifications to the car can generate gains of a few milliseconds per lap, making the difference at the finish line. A great deal of effort goes towards ensuring that the slipstream works exactly where it is supposed to.
At Sauber Motorsport AG, 140 employees are involved in working on the flow field, simulation and wind tunnel tests. This team includes designers, mechanics and track data analysts. The new diffuser and the reduced wing elements have significantly changed the aerodynamics of the new Alfa Romeo F1® Team ORLEN C42.
A successful 20-year partnership: Brütsch/Rüegger Tools and Sauber Motorsport
Brütsch/Rüegger Tools has been a Tools & Quality partner of Sauber Motorsport for 20 years. Our specialists support the team at Hinwil, Switzerland, by providing services, product consultations and broad sets of branded products for the measurement, manufacturing and assembly sectors. The company, which employs 550 people, is also one of the largest customers of chemical products at Brütsch/Rüegger Tools and purchases a wide range of products, including adhesives, cleaning products, thread locks, screw pastes, retaining compounds, cold sprays, cooling lubricants and sealing coats. Read more about our chemical product sets in the article: 4 facts about why our chemistry works.
This year, Sauber Motorsport is marking the 30th Formula 1 season with celebrations for another anniversary. Alfa Romeo is championing a completely new driver combination of Finnish driver Valtteri Bottas and the Chinese newcomer Zhou Guanyu. Brütsch/Rüegger is looking forward to the future partnership and wishes the team every success this season!
2022 —Return of the ground effect
However, the brilliant new feature is not as easily visible: After several decades, Formula 1 is returning to the ground effect and once again allowing the use of the Venturi tunnel — open air ducts that influence the downforce, i.e. the grip on the ground. The Venturi effect is generated by the air flowing under the car through two large cut-outs in front of the sidepods via two tunnels. The tunnel roofs, which slope down to the rear, force the air against the road surface and accelerate it.
In conjunction with the diffuser, the aim is to reduce the amount of air turbulence behind the car that puts approaching vehicles at a disadvantage. The exciting thing is: This effect should facilitate overtaking.
Initial tests in Barcelona showed that the familiar effect of "porpoising" has reappeared due to the ground effect. This "porpoising car" phenomenon is caused by a flow break in the underbody at peak speeds. It needs to be anticipated and compensated by the suspension.
Striking a balance between peak speed and downforce
Once the engine, chassis and suspension have been designed, the main focus of the work lies in honing the aerodynamics. The aerodynamics engineers adapt the Formula 1 car to the local conditions from one race to the next, to get the most out of the flow technology. For each track, the aim is to strike the perfect balance between peak speed—depending on the air resistance—and downforce. The goal: Maximum output with minimum air resistance.
While a strong downforce allows for higher cornering speeds and shorter braking distances, a low air resistance increases, among other things, peak speed. The most important factor in the aerodynamic adjustments is the track layout, as Alessandro Cinelli, Head of Aerodynamics at Sauber Motorsport AG, explains: "A lot of long straights, such as those at Monza, require a minimum of drag and so these are driven on with flat-wings. Tracks full of corners, such as Monaco, on which air resistance plays a minor role, are driven with steep wings". The climatic conditions—warm air flows behave differently from cold ones—and the driver's driving style, including how confident they are feeling, also constitute influencing factors.
A comparison helps to better visualise the extent of the forces: While the lift of a passenger car travelling 250 km/h is around 30 kilogrammes, a Formula 1 car generates a downforce of as much as 600 kilogrammes at 180 km/h. This force generated by the aerodynamics is needed to keep the car on the ground. If the Alfa Romeo C42 had been travelling without any downforce-generating parts, it would lift at around 180 km/h. In other words: Thanks to the aerodynamic parts, the car could even drive upside-down on the top of a huge tube.
Generating downforce at the wings and diffuser. (Image source: Sauber Motorsport)
Wind tunnel:
Ultra-modern Model Motion System
The central tool for improving aerodynamics is the wind tunnel, and one of the most modern tunnels can be found at Sauber Motorsport in Hinwil, Switzerland. Using the millimetre-precise Model Motion System, it is possible to test the racing car's behaviour in inclined positions as well. While the "rolling road" can be rotated up to 10 degrees from the wind direction, it is also possible to lift or lower the car via a suspension device. This is done to simulate inclined air flows that occur in cornering, acceleration or braking positions. Various scales mounted on the car are used to measure the prevailing wind forces. The exhaust gases are also simulated: Air is blown in at high pressure to simulate the flow coming from the exhaust. But this variable no longer plays a dominant role in the latest generation of F1 cars.
The laws of aerodynamics do not apply everywhere. Changes in the regulations by the Fédération Internationale de l'Automobile (FIA) have often resulted in changes needing to be made, such as back in the 1980s when strong downforce was stopped to facilitate driving and increase safety. Incidentally, the FIA now also limits the number of hours that can be spent in the wind tunnel. Since 2021, this has depended on the current classification spot. The better a team's classification, the fewer hours that are available.
Virtual wind tunnel: CFD simulation
For this reason, only the most important issues are tested in the wind tunnel. Data from CFD (Computational Fluid Dynamics) simulations is obtained to determine what these issues are. This air flow simulation is also called a virtual wind tunnel. Alessandro Cinelli continues: "We use the CFD simulation specifically to obtain information and measurement data at critical points, in order to make calculations".
Meshing is the generation of volume or surface mesh, which is used not only to optimise aerodynamic parts, but also to cool the brakes or engine environment, or for general cooling of the engine, hydraulics, gearbox and electronics as well as fluids such as water or fuel. For such simulations, the CFD specialists use a volume mesh of hundreds of million cells and a surface mesh of several million cells.
To support the flow dynamics in turn, the aerodynamic modifications also use car data from previous races. However, the C42 is a completely new model, so this is not the case this season. Nevertheless, the virtual wind tunnel, which provides increasingly precise predictions for real flow operations under different conditions, is gaining in importance. CFD data and visualisations are instantly available to the CFD team. However, measurements in the real wind tunnel are still required to verify the results for more complex optimisation projects. Alessandro Cinelli sums it up thus: "The wind tunnel brings us closer to reality, but nothing is better than reality itself".
In focus: Maximum precision and flawless quality
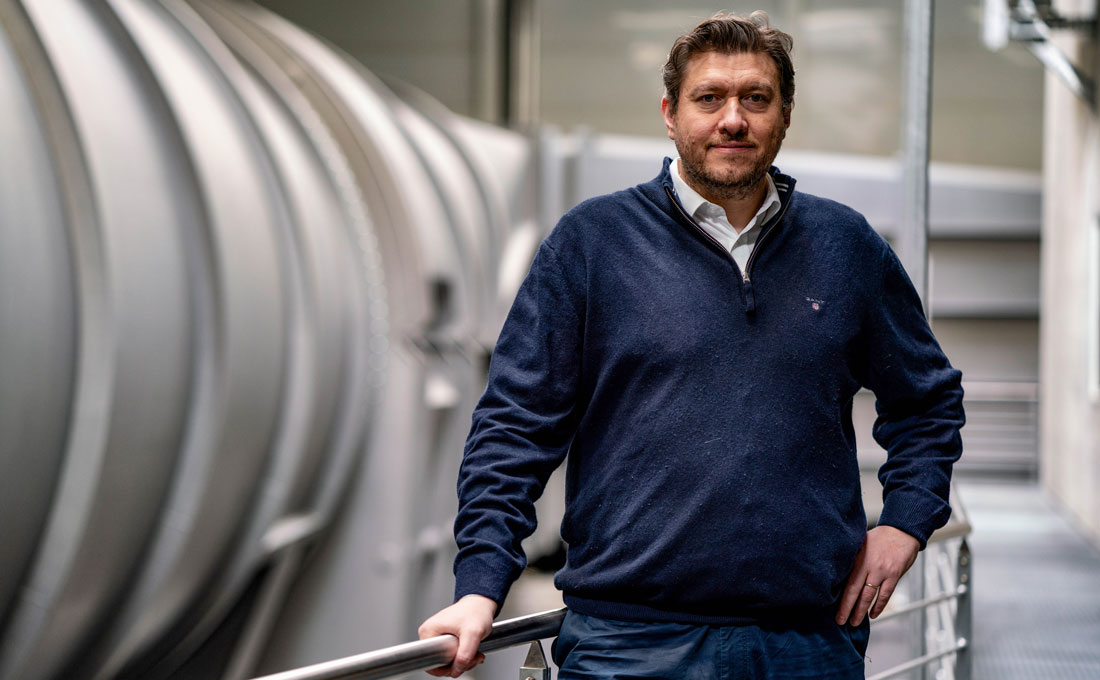